Program szkolenia
- Kluczowe pojęcia i zasady efektywnego zarządzania procesami
- Marnotrawstwo: definicja, typy i źródła
- Efektywność procesów produkcyjnych – co ją warunkuje?
- Wprowadzenie do filozofii Lean Manufacturing
- Historia i założenia koncepcji Lean
- Lean a zarządzanie zapasami: synergia dla sukcesu
- Metody diagnozowania marnotrawstwa
- Analiza przepływu wartości (Value Stream Mapping – VSM)
- Techniki obserwacji procesów produkcyjnych
- Praktyczne przykłady marnotrawstwa
- Nadprodukcja, nadmierny transport, nadmiarowe zapasy
- Niewykorzystany potencjał pracowników i przestoje
- Wprowadzenie narzędzi eliminacji strat
- 5S jako baza do poprawy organizacji pracy
- Kaizen – małe kroki wielkich zmian
- Projektowanie procesów o wysokiej efektywności
- Balansowanie linii produkcyjnej
- Minimalizacja czasu cyklu
- Zastosowanie standardów pracy
- Tworzenie i wdrażanie standardowych procedur operacyjnych (SOP)
- Standaryzacja jako narzędzie ciągłego doskonalenia
- Zarządzanie przepływem pracy
- Wykorzystanie techniki Kanban
- Eliminacja wąskich gardeł i usprawnianie przepływu
- Rola i znaczenie zarządzania zapasami
- Koszty związane z utrzymywaniem zapasów
- Wpływ zapasów na płynność finansową firmy
- Narzędzia i metody zarządzania zapasami
- System Just-In-Time (JIT) – założenia i wdrożenie
- Analiza ABC i XYZ w zarządzaniu zapasami
- Prognozowanie popytu i planowanie zaopatrzenia
- Jak unikać nadmiarów i niedoborów?
- Zastosowanie modeli matematycznych w planowaniu
- Etapy wdrożenia zmian w procesach produkcyjnych
- Przygotowanie organizacji na zmiany
- Testowanie i doskonalenie wprowadzonych rozwiązań
- Przykłady wdrożeń optymalizacyjnych w różnych branżach
- Case study – analiza rzeczywistych przykładów sukcesu
- Bariery we wdrażaniu zmian i sposoby ich pokonywania
- Opór pracowników wobec zmian
- Rozwiązywanie problemów w trakcie implementacji
- Wskaźniki efektywności procesów (KPI)
- Kluczowe metryki dla zarządzania produkcją
- Jak analizować i interpretować dane produkcyjne?
- Metody monitorowania procesów
- Audyty produkcyjne i ocena wdrożonych zmian
- Wizualizacja danych – dashboardy produkcyjne
- Ciągłe doskonalenie jako strategia organizacji
- Cykl PDCA (Plan-Do-Check-Act)
- Regularne analizy i aktualizacja strategii optymalizacyjnych
Grupa docelowa i idea szkolenia: Optymalizacja procesów produkcyjnych – eliminacja marnotrawstwa i zarządzanie zapasami
Grupa docelowa szkolenia “Optymalizacja procesów produkcyjnych – eliminacja marnotrawstwa i zarządzanie zapasami” to managerowie produkcji, inżynierowie procesu, specjaliści ds. zarządzania jakością oraz liderzy zespołów produkcyjnych. Osoby odpowiedzialne za optymalizację procesów w firmie, redukcję marnotrawstwa oraz skuteczne zarządzanie zapasami i planowanie produkcji. Uczestnikami mogą być także członkowie zespołów projektowych zajmujących się wdrażaniem usprawnień w procesach produkcyjnych, którzy chcą pogłębić swoją wiedzę i umiejętności w zakresie efektywnego zarządzania procesami.
Idea szkolenia “Optymalizacja procesów produkcyjnych – eliminacja marnotrawstwa i zarządzanie zapasami” opiera się na przekazaniu kompleksowej wiedzy dotyczącej identyfikacji i eliminacji marnotrawstwa w procesach produkcyjnych oraz optymalizacji tych procesów w celu zwiększenia efektywności i redukcji kosztów. Szkolenie ma na celu nie tylko teoretyczne zrozumienie kluczowych pojęć i narzędzi, takich jak Lean Manufacturing, Just-In-Time oraz zarządzanie zapasami, ale także umożliwia uczestnikom doświadczenie praktycznych aspektów poprzez symulację produkcyjną. Dzięki temu uczestnicy będą mogli nie tylko analizować i diagnozować istniejące problemy, ale również proponować i wdrażać skuteczne rozwiązania w swoich organizacjach, promując kulturę ciągłego doskonalenia i systematycznego usprawniania procesów.
Optymalizacja procesów produkcyjnych – eliminacja marnotrawstwa i zarządzanie zapasami: korzyści ze szkolenia
- Zwiększenie innowacyjności: Wspólne dążenie do ciągłego doskonalenia sprzyja wdrażaniu nowych rozwiązań technologicznych i organizacyjnych. Organizacja zyskuje nowoczesne procesy, a pracownicy uczestniczą w rozwijaniu i testowaniu innowacji.
- Lepsza komunikacja i współpraca zespołowa: Optymalizacja procesów wymaga skutecznej wymiany informacji i współdziałania między działami. To poprawia relacje w zespole, eliminuje nieporozumienia i buduje kulturę współpracy.
- Zwiększona elastyczność organizacji: Wprowadzenie bardziej efektywnych procesów umożliwia szybsze reagowanie na zmieniające się warunki rynkowe, co stabilizuje sytuację firmy. Pracownicy zyskują pewność, że firma potrafi dostosować się do nowych wyzwań, co wpływa na ich bezpieczeństwo zawodowe.
- Wyższa satysfakcja klientów: Lepsza jakość produktów, terminowość dostaw i szybsze reagowanie na potrzeby klientów przekładają się na większą lojalność odbiorców. Zadowolenie klientów wpływa na stabilność firmy i tworzy pozytywne środowisko pracy dla zespołu.
- Rozwój kultury ciągłego doskonalenia (Kaizen): Zarówno organizacja, jak i pracownicy wspólnie kształtują kulturę, w której dąży się do stałego usprawniania procesów. Taki model pracy sprzyja zarówno wzrostowi efektywności firmy, jak i rozwijaniu kompetencji pracowników.
Korzyści dla organizacji
- Redukcja kosztów operacyjnych: Dzięki skutecznej identyfikacji i eliminacji marnotrawstwa organizacja znacząco obniża koszty produkcji, magazynowania i logistyki. Optymalizacja procesów pozwala zminimalizować straty materiałowe, zużycie energii oraz koszty związane z nadprodukcją, co bezpośrednio przekłada się na poprawę rentowności.
- Zwiększenie wydajności i efektywności procesów: Usprawnione procesy produkcyjne prowadzą do lepszego wykorzystania zasobów, szybszej realizacji zleceń oraz ograniczenia przestojów. To pozwala organizacji szybciej reagować na zmieniające się potrzeby rynku i zwiększyć moce produkcyjne bez konieczności ponoszenia dodatkowych inwestycji.
- Poprawa jakości produktów i usług: Eliminacja błędów produkcyjnych i wprowadzenie standardów pracy wpływają na zwiększenie jakości oferowanych produktów. Dzięki temu organizacja minimalizuje liczbę reklamacji i zwrotów, co buduje pozytywny wizerunek marki oraz zwiększa satysfakcję klientów.
- Lepsze zarządzanie zapasami: Wdrożenie metod takich jak Just-In-Time pozwala na zmniejszenie nadmiarowych zapasów oraz ograniczenie kosztów magazynowania. Organizacja utrzymuje optymalny poziom zapasów, co zwiększa płynność finansową i redukuje ryzyko przeterminowania lub uszkodzenia towarów.
- Wzrost konkurencyjności na rynku: Organizacja, która efektywnie zarządza procesami i eliminuje marnotrawstwo, szybciej dostosowuje się do zmian rynkowych i oczekiwań klientów. To umożliwia wprowadzanie innowacji, szybsze reagowanie na trendy i budowanie przewagi konkurencyjnej.
Korzyści dla pracowników
- Lepsze zrozumienie procesów pracy: Pracownicy zdobywają wiedzę na temat funkcjonowania procesów produkcyjnych i narzędzi optymalizacyjnych, co pozwala im świadomie uczestniczyć w usprawnianiu codziennych działań i lepiej rozumieć wpływ swojej pracy na wyniki firmy.
- Poprawa warunków pracy: Eliminacja zbędnych czynności, nieefektywnych procesów oraz źródeł marnotrawstwa prowadzi do zmniejszenia obciążenia fizycznego i psychicznego. To przekłada się na większy komfort pracy oraz bezpieczeństwo na stanowisku.
- Rozwój umiejętności analitycznych i problem-solving: Pracownicy uczą się identyfikowania problemów, analizowania przyczyn i wdrażania skutecznych rozwiązań. Dzięki temu stają się bardziej samodzielni i lepiej radzą sobie z codziennymi wyzwaniami.
- Większe zaangażowanie w procesy decyzyjne: Udział w procesach optymalizacyjnych zwiększa poczucie odpowiedzialności za wyniki firmy. Pracownicy mogą aktywnie zgłaszać swoje pomysły i wpływać na wprowadzane zmiany, co buduje ich motywację do pracy.
- Stabilność zatrudnienia: Zwiększenie efektywności i rentowności organizacji zmniejsza ryzyko redukcji zatrudnienia. Pracownicy mogą czuć się bezpieczniej, wiedząc, że firma lepiej radzi sobie na rynku i jest mniej narażona na kryzysy ekonomiczne.
Metody wykorzystywane podczas szkolenia
Warsztaty praktyczne
Uczestnicy angażują się w rozwiązywanie rzeczywistych problemów produkcyjnych poprzez pracę w grupach, analizowanie procesów i wdrażanie wybranych narzędzi optymalizacyjnych. Dzięki praktycznym ćwiczeniom zdobywają doświadczenie w identyfikacji marnotrawstwa i projektowaniu usprawnień.
Studium przypadku
Analiza autentycznych przykładów firm, które skutecznie wdrożyły metody optymalizacji procesów i zarządzania zapasami. Uczestnicy omawiają zastosowane rozwiązania, identyfikują kluczowe czynniki sukcesu oraz potencjalne zagrożenia, co pozwala lepiej zrozumieć praktyczne aspekty zarządzania zmianą.
Symulacje procesów
Realistyczne ćwiczenia odzwierciedlające rzeczywiste warunki produkcyjne, pozwalające uczestnikom na testowanie narzędzi Lean Manufacturing, 5S czy Just-In-Time. Symulacje umożliwiają analizę przepływu pracy, wykrywanie wąskich gardeł oraz ocenę efektów wprowadzonych usprawnień.
Ćwiczenia indywidualne i zespołowe
Zadania praktyczne, które pozwalają na utrwalenie wiedzy i rozwijanie umiejętności analitycznych. Uczestnicy indywidualnie i zespołowo rozwiązują problemy, co sprzyja kreatywności, samodzielności oraz współpracy w zespole.
Trenerzy
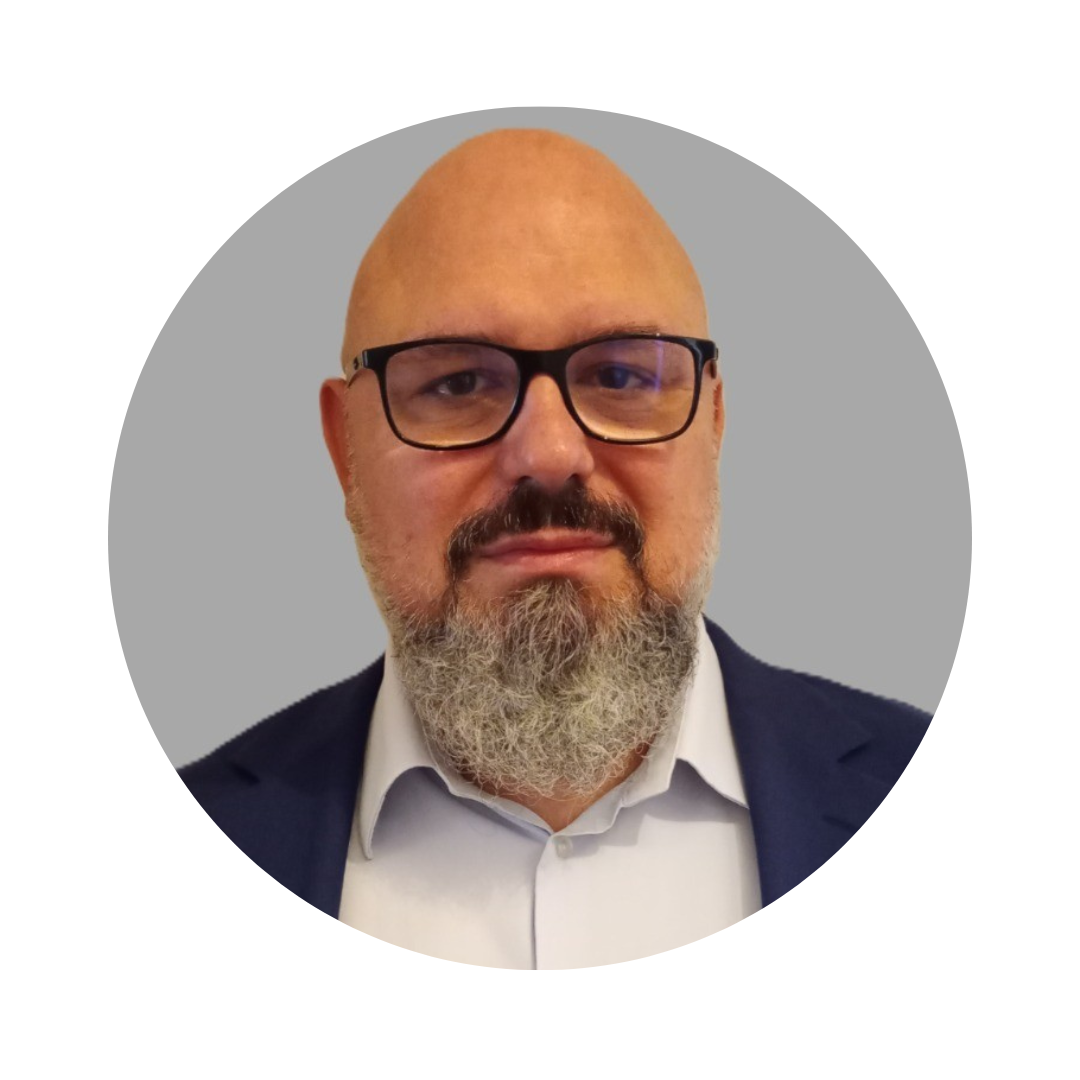
Marian Krzeszowski
Specjalizuje się w zarządzaniu produkcją oraz optymalizacji procesów. Przeprowadził dotychczas ponad 650 dni szkoleniowych, samodzielnie dla firm zewnętrznych i jako współpracownik dla firm szkoleniowych. Dodatkowo przeprowadziłem 700 dni prowadząc lub uczestnicząc w projektach doradczych. Posiada wiedzę z zakresu optymalizacji procesów produkcyjnych oraz logistycznych. Jego umiejętności obejmują wdrażanie narzędzi Lean Manufacturing, takich jak 5S, SMED, Kanban oraz MTM. Dodatkowo, ma doświadczenie w mapowaniu procesów, co pozwala na szczegółową analizę i doskonalenie działań produkcyjnych. Specjalizuje się w pracy zespołowej, zarządzaniu projektami oraz wprowadzaniu zmian organizacyjnych, a także uczestniczyła w licznych szkoleniach, takich jak REFA, MTM czy 5S. Uczestniczył w wielu projektach optymalizacji procesów produkcyjnych w renomowanych firmach, takich jak Volkswagen, Cersanit, Elektrolux oraz Dell. Projekty obejmowały wdrażanie nowych koncepcji logistycznych, analizę czasów pracy oraz poprawę ergonomii i efektywności procesów produkcyjnych. Posiada doświadczenie na różnych stanowiskach, od specjalisty ds. produkcji, przez kierownika ds. optymalizacji, aż po koordynatora Lean Manufacturing. Zrealizował wiele projektów optymalizacyjnych, zdobywając uprawnienia trenera REFA oraz praktyczne zastosowanie metodologii w licznych projektach. Jego osiągnięcia obejmują wdrożenia, które zwiększały konkurencyjność przedsiębiorstw poprzez redukcję kosztów, zwiększenie wydajności oraz optymalizację procesów.
Opinie
Profesjonalnie zorganizowane szkolenie
Interesujące i bardzo profesjonale szkolenie
Współpraca